
Thankfully the vespino model that I have take two 6203 bearings which were easy enough to get from my local bearing shop. The first step is to get the bearing on the small shaft side on.
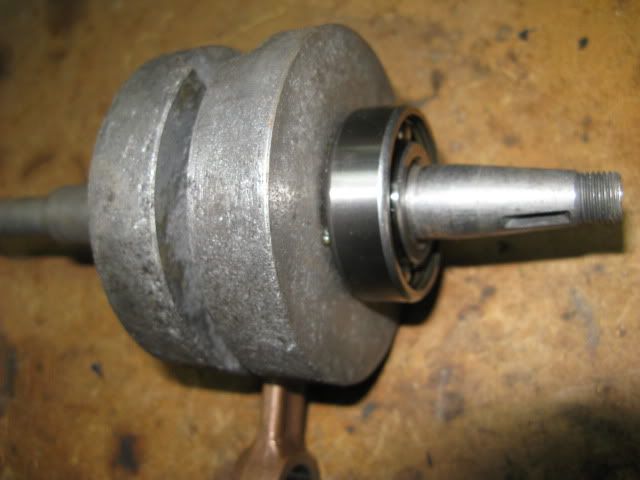
This can be done easily by putting the crank in the freezer and heating the bearings in an oven. I cook mine till tender at a temp of 300. (This is due to metal expanding when hot and shrinking when it gets cold) Then you get gloves and just drop the bearing on the shaft and whalla! If the temperatures were different enough the bearing should slide all the way down to the base of the shaft and you'll hear a "clunk." If not you need to work quickly to force it all the way down.
Next you have to maneuver the crank into the case. You have to make a plan of attack because like before we're going to be heating and cooling things again. Because I forgot to take a better picture of this process I'll borrow a picture from my friends at vespinos.net.

Once you have a game plan, you then need to start by heating the case to receive the bearing...and put the crank in with the frozen foods.
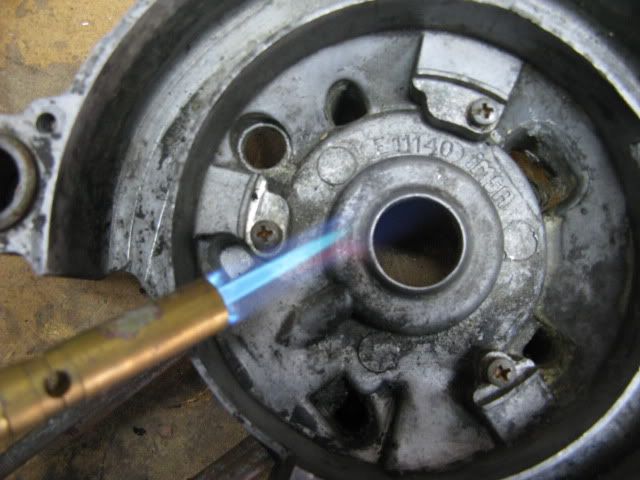
3-2-1 go. Work quickly to wrangle that crank into place. You can tap the long crankshaft with a rubber mallet to really make sure the bearing is seated properly. It should look like this.
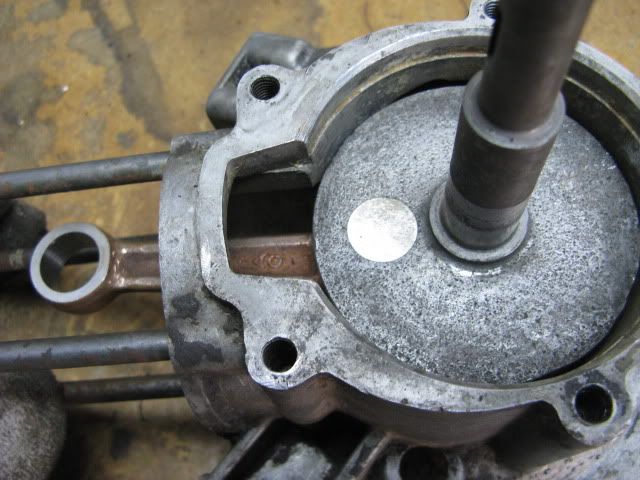
Next you need to install the bearing into the long single sided subframe thing (which strangely is the other case half). This time you need to use reverse thinking by heating the opening and freezing the bearing.
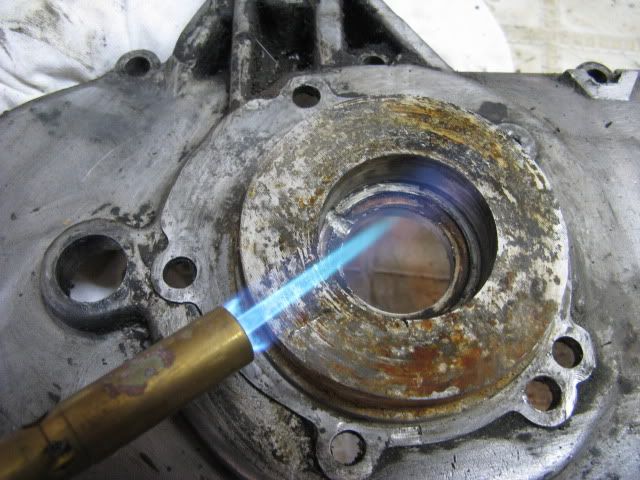
Even after doing this, I had a hard time getting my bearing to drop in right...it might be because my case is a little dirty...I used a hammer to tap it into place.
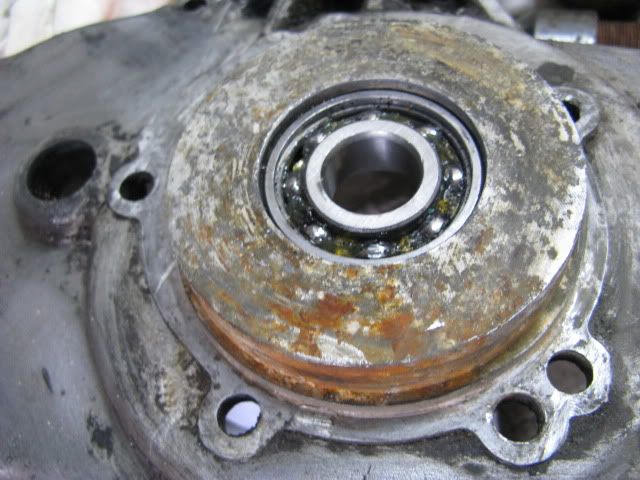
Now its time to join out cases! First things first though. When using a gasket for a Spanish moped that wasn't supposed to leave Spain...it might be a good idea to make copies of your gaskets for later use...
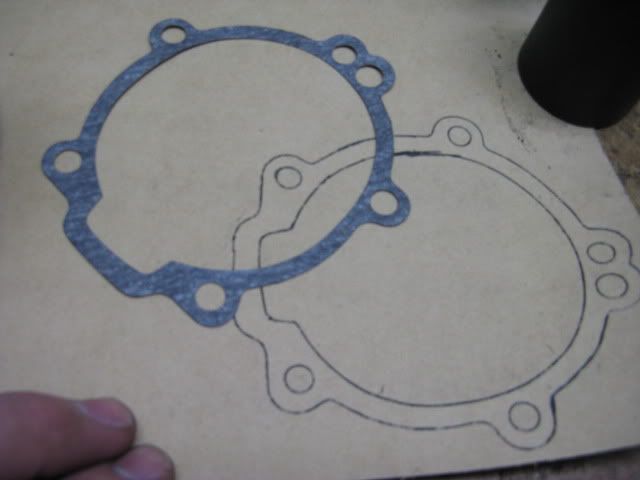
I always add a little Right Stuff to help with the seal...place the gasket and continue heating and cooling! Heat the inside of the bearing in the subframe and cool the half with the crank already installed.
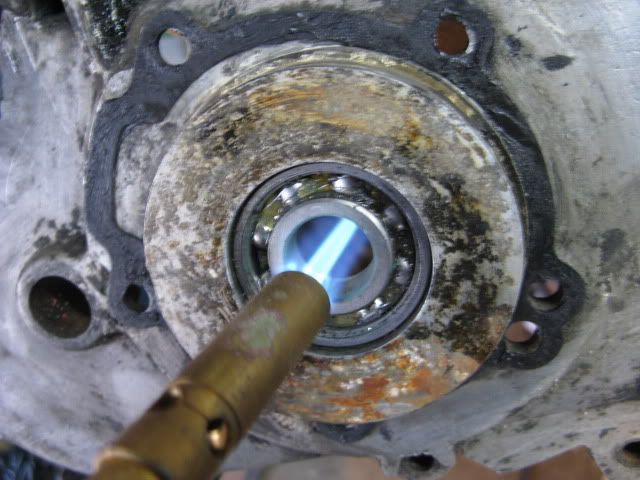
Then join the halves and tighten down the bolts in a cross patter so as not to pinch the crank webbing.
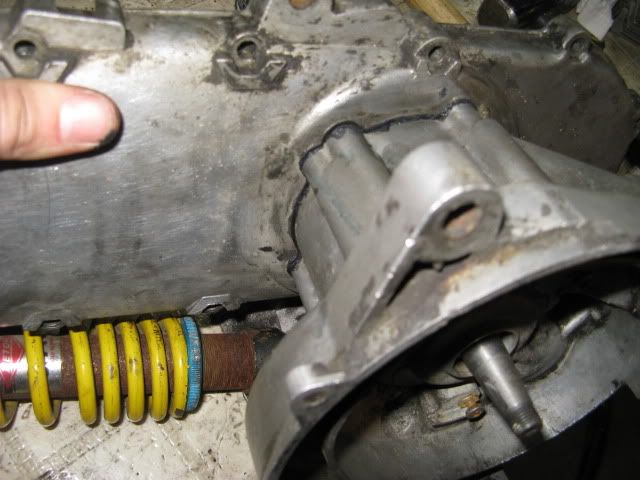

If installed properly the crank should still spin freely. Lastly, once everything has cooled down, install the seals. I used a handle bar to ensure that it was snugly in place.
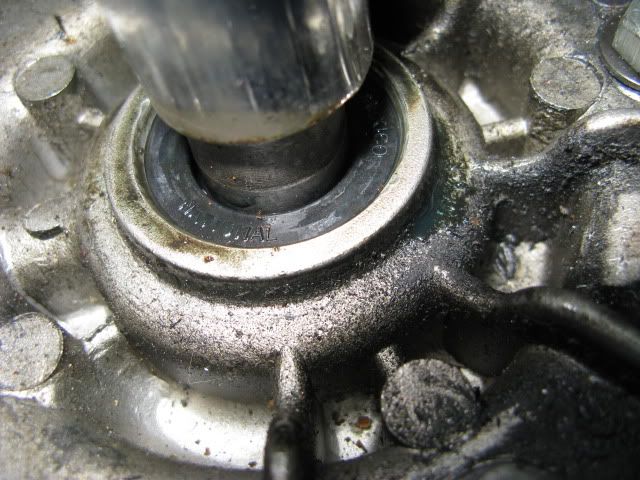
nice! I was going to ask how this was progressing. Did you end up getting a whole new crank or just the con rod?
ReplyDeleteoh yeah. how did i forget to mention that. You can't buy a complete new crank (or at least its super hard) because they never made new cranks for this model. apparently my engine is one of the last in this particular series and they made some changes to it. One being that it takes 2 of the same sized bearings and 2 that the stroke is different. If you wanted a new crank you would have to buy a crank for an older model and change the conrod. I just bought a new conrod and found a motorcycle shop to press it in for me. they sandblasted the webbings, cleaned them up, and balanced it. like new. so yeah...yet another reason this project has been on hold. but hopefully it'll get rolling pretty fast now.
ReplyDeleteyes!
ReplyDeleteholy moly jason. this is so crazy. you can guarantee that you are the only one in the united states doing this right now. which is awesome!!!
ReplyDeletenice! awesome to see progress on this. good general writeup on how to do bearings too.
ReplyDeleteever get around to building that simo motor? cant wait to see that sucker finished.
Actually...Sadly...the rest of my unused simo tech might go up for sale to fund a European get-a-way...still chewing on the idea.
ReplyDelete